RIFAST Equipment
Press Shop Solutions
Preventing Offline Processes and Improving Efficiency
Punching heads are designed to support customer fastener installation requirements specific to configurations of the stamping. Punching heads can be mounted above or below the strip and supports nut or stud installation for each press stroke. Additionally, the distribution system, in-die feeding system, and junction box are used as support for the punching heads. The distribution system allows multiple punching heads to be fed. The in-die feeding system supplies the fasteners to the punching head equipment. Lastly, the junction box allows for communication between the punching head and the feeding system and reduces press change-over time during removal or installation of the press tool. These pieces of equipment are designed to make fastener installation easier for you when using RIFAST Fasteners.

RIFAST Equipment
Press shop solutions
Preventing Offline Processes and Improving Efficiency
VMM/VMB
Punching head vertical
The robust, reliable and high-standardized platform for all RIFAST bolt and nut functional elements.
Proven in-die punching heads for progressive dies, transfer dies, tandem dies and presses
CLASSIC FIT: in-die punching heads for bolts (VMB) and nuts (VMM)
VKM
Punching head compact
The compact, robust, weight optimized and flexible platform for RIFAST nut functional elements.
Proven in-die punching heads for progressive dies, transfer dies, tandem dies and presses.
COMPACT FIT: in-die punching head for nuts (VKM)
VQM
Punching head horizontal
The robust and compact platform for horizontal insertion of RIFAST nut functional elements.
Proven in-die punching heads for progressive dies, transfer dies, tandem dies and presses.
COMPLEX FIT: in-die punching head for horizontal insertion of nuts (VQM)
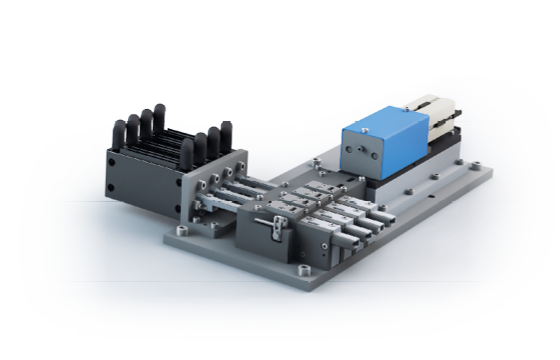
VDM
Distribution system
The compact, robust and cost optimized platform for installation of up to 16 RIFAST nut functional elements in one press stroke.
The distribution system (VDM) is the right choice for components with many of the same nut functional elements. In combination with a 4-lane standard feeding unit for nuts (ZEM), up to 4 distribution systems can be supplied with elements. With up to 4 compact active units, these can provide a maximum of 16 nuts for a joining process.
The RIFAST Distribution
system Advantage
ZEM/ZEB
In die feeding system
The robust, reliable, high-standardized and fast feeding system platform in front of the press for all RIFAST bolt and nut functional elements. Up to 60 strokes/min.
For in-die processes under the press there are two types of feeding units available. The widely adopted feeding unit which is placed in front of the press or the feeding unit which can be placed on the press table.
The RIFAST feeding
unit advantage
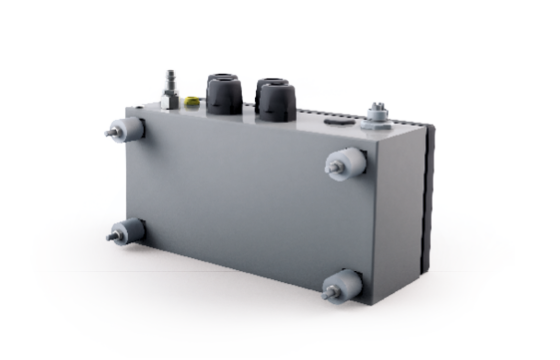
WZV
Junction box
The compact, robust and flexible junction box enables a quicker and more flexible tool setup from punching heads to feeding unit.
The junction box is used for an easier routing and connecting from the punching heads inside the tool to the feeder. The short multifunction hoses stay always connected at the punching heads for a faster tool set-up and a perfect pneumatic supply.
Because of less moving hoses from the feeder to the tool ensures a more reliable process. Due to the compact design it is possible to connect up to 4 punching heads with one WZV at one feeder. All signals from the punching heads are send directly via bus system to the feeder.
The RIFAST Junction
box Advantage
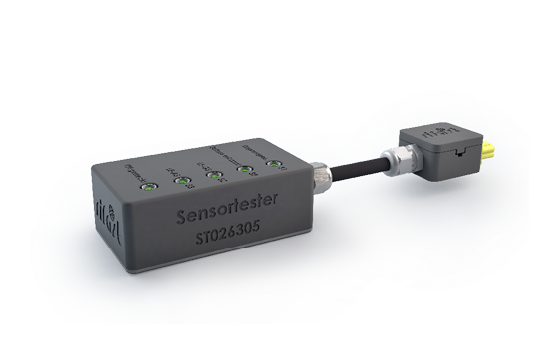
Sensor tester
For sensors in the punching head
During fault analysis and maintenance it is necessary to check the sensors in the punching head. Easy access to the punching head and the feeding unit is often not possible. With the small and handy sensor tester, sensors can be tested without removing the punching head and without a connection to the feeding unit.
Sensor Tester Advantage